IT OT Convergence – Benefits and Challenges in Manufacturing
Information technology (IT) and operational technology (OT) have long existed in their separate spheres. Each had its own network, objectives, and requirements. And, until relatively recently, this separation was perfectly fine.
However, the Industrial Internet of Things (IIoT) is changing the game and tearing down old silos. Complex machines are now integrating with network sensors and being managed by advanced analytics software, blurring the line between where IT ends and OT begins.
When IT and OT join forces, organizations unlock several benefits from process automation and business intelligence to a simplified system for ensuring regulatory compliance. In this article, we’ll look closely at IT-OT convergence and why it matters.
We’ll also touch on some of the key benefits that IT-OT unity offers.
How Does IIoT Bring IT and OT Together?
Before we get into the nitty-gritty, let’s quickly go over an IT-OT convergence definition.
IT-OT convergence is a term that refers to the integration of information technology systems (which handle computing and data processing) and operational technology systems (which manage and control industrial operations).
Traditionally, IT is responsible for creating, storing, and securing an organization’s data. At the same time, OT focuses primarily on processes that take place in the physical world–think managing productivity, people, and machinery.
Today, more and more organizations are embracing Industrial IoT (IIoT) technologies like smart meters, automated asset distribution systems, and self-monitoring transformers. We’re now seeing production lines and farm equipment outfitted with sensors.
The rise of these new technologies has created a need for organizations to optimize how machines, applications, and infrastructure collect, transmit, and process data. Done right, convergence gives businesses the ability to fix critical issues faster, make informed business decisions, and scale processes across both physical and virtual systems.
Ways Industries Benefit from OT-IT Convergence
The industrial internet of things generates unimaginable amounts of data collected from sensors, software, and large assets that could be spread across several locations.
With so many moving parts involved, IT-OT convergence gives organizations a strong foundation for improving internal processes, business decisions, and productivity.
Here are some of the IT-OT convergence benefits manufacturing companies can expect:
Simplified Process Control
IIoT platforms are increasingly replacing bulky manufacturing execution systems (MES software) and their related applications–which are typically used for inventory tracking, production maintenance, and quality control.
These activities are distributed across both OT and IT, so when each department runs as a separate entity, there’s a missed opportunity to control and optimize manufacturing processes.
Real-Time Visibility
As a result of increased connectivity offered by IIoT technologies, smart manufacturing systems generate a ton of data.
Consider how many sensors might be found on the factory floor alone. Then, look at all of the potential scenarios digital twin software can provide, business analytics from CRMs, and inventory planning software; the list is endless.
With IT-OT integration, data-sharing happens across the entire organization, allowing decision-makers to analyze machine-generated data in real-time.
In the past, aggregating data from various machines, sensors, databases, and gateways was a manual effort that required compiling data from disparate sources and attempting to analyze that information as a single unit.
Eliminating Unplanned Downtime
IT-OT integration is also helping organizations combat the issues associated with unplanned downtime–including equipment failures and profit losses–by digitizing the maintenance process and pulling insights directly from the factory floor. By monitoring machine performance, OT and IT teams can monitor equipment for early signs of trouble, and act accordingly.
Why OT-IT Convergence Matters
Why does convergence matter? Well, for starters, convergence matters because success in today’s connected industrial landscape hinges on collaboration. IIoT is changing how manufacturers work, blurring the lines between IT and operations.
For example, IT pros might now spend more time working with equipment on the factory floor, while OT teams will need to bone up on cybersecurity and networking best practices.
IT-OT convergence isn’t about turning IT pros into heavy machinery operators or plant engineers into data scientists. Rather, it’s about creating a strategy that bridges the gap and allows organizations to improve operational performance by working around a unified set of objectives and KPIs.
Technologies Make IT-OT Convergence Possible
According to a Gartner survey, organizations are eager to integrate IIoT and IT technologies, however, many organizations lack the skills, expertise, or IT-OT alignment required to deliver the best possible outcomes.
Luckily, we’re beginning to see new technologies emerge in response to these challenges–whether that means democratizing development or making it easier to understand massive amounts of data, here are a few innovations making convergence a reality for more manufacturers.
- No Code Applications. No code or low-code applications are used to connect IIoT devices, sensors, and machines, as well as the humans that work with them on the factory floor. These programs are designed for human users without a background in coding, offering an easy way for OT teams to create applications that work for the assembly line without having to learn how to code.
- Digital Twins. Digital twin software allows organizations to build virtual replicas of physical objects like heavy machinery or entire manufacturing systems in a digital environment. This technology allows manufacturers to see how environmental factors, changes to the production cycle, and adverse events might impact product quality or productivity.
- Augmented Reality. Augmented reality tools aren’t exactly at the forefront of innovation today–after all, Caterpillar has been using AR for inspections since 2015. That said, AR technology is improving all the time. Today, organizations can use AR in a connected system to oversee factory operations remotely, provide enhanced training simulations, and guide technicians through complex repairs.
- Edge Computing. The edge is increasingly considered to be the intersection where OT and IT meet. In the typical IIoT system, data is generated and collected by OT before sending it along to IT for analysis in the data center or the cloud. Edge computing allows organizations to process data in real-time, rather than waiting for it to show up in the cloud, allowing organizations to convert machine-generated data into actionable insights quickly.
Impact of Convergence on Industrial Control Systems Security
IT departments are well-versed in everything that can go wrong when a network is compromised–think reputational damage, a loss of customer trust, fines, and even the possibility of a lawsuit.
Traditionally, OT has been about protecting physical processes–ensuring uptime, efficiency, and worker safety. However, the stakes are even higher when OT goes digital. Now, we’re looking at a situation where cybersecurity and actual physical security are the same. For example, a cyberattack can take down power plants, waste management systems, food processing plants, and transportation networks.
As such, an IT-OT gap can lead to a full spectrum of potential disasters, including safety hazards, downtime, sabotage, and financial losses.
Hackers often infiltrate ICS systems using both generic malware as well as malware designed for the express purpose of taking down critical systems. As a result, IIoT adopters are especially vulnerable to denial-of-service (DoS) attacks that bring industrial operations to a standstill, ransomware attacks, or acts of sabotage where rivals break in to steal a business’ confidential data.
It’s also worth mentioning that the human-machine interface (HMI) that connects human operators to the ICS is also connected to the IT network. This means that HMIs are also susceptible to vulnerabilities, default settings, weak poor password management practices, unsupervised session management, and unsecured communication protocols not meant for the HMI work itself.
Wrapping Up
IT-OT integration might seem overwhelming. However, it’s an essential first step for any organization that wants to realize the benefits of IIoT. While uniting two departments who have historically done their own thing comes with a whole range of challenges, benefits like streamlined processes, interoperability, and collaborative decision-making make IT-OT convergence well worth the effort.
[adinserter name=”IIoT Closing”]
Recent blog posts
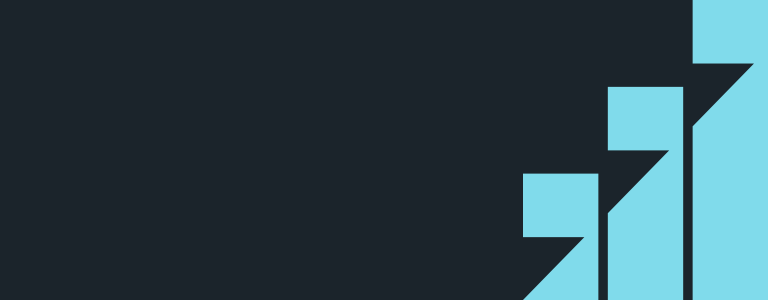
Stay in Touch
Keep your competitive edge – subscribe to our newsletter for updates on emerging software engineering, data and AI, and cloud technology trends.